Buyer’s Guide
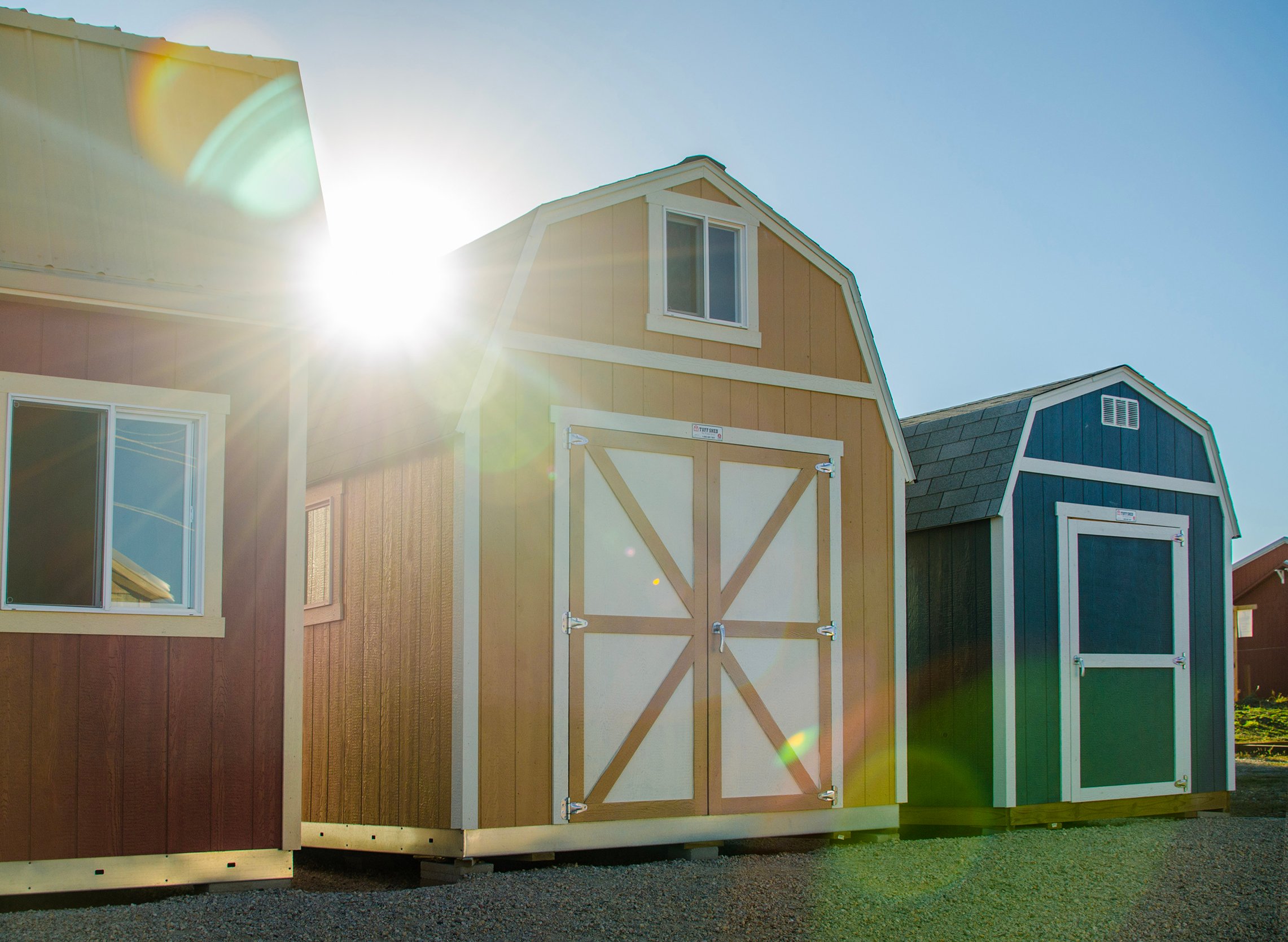
Frequently asked questions and other helpful resources about Tuff Shed products, processes, and customer care.
Pre-Purchase
Learn about Tuff Shed products and processes. Compare building styles, sizes, upgrades, and prices.
Choosing the right model for you
Where should I start with choosing the right model?
Most of our customers have a general idea of what they want the building to look like, and that really starts with the roof shape. Tuff Shed offers buildings in barn-style, ranch-style, and lean-to-style roofs, and we separate our buildings into a good-better-best assortment of the Garden Series®, Premier Series®, and Premier PRO Series(TM). From there you can start to focus on the features that are important to you, such as wall height, door placement, roof and siding material, and warranty length. Check out the handy comparison feature on the products page of this website, or visit one of our sales teams to learn more.
Is there any visual guidance on available products?
Yes! Check out our products page on this site, or the PDF here which compares elements like roof shape and pitch, door openings and placement, eave types, and warranty lengths.
What size can I get?
Most of our buildings can be configured in a variety of sizes, and are designed so that sizing is a sliding scale in 2-foot increments as it relates to width and length. Start with our online configurator to see size availability by model, and consult your Tuff Shed rep if you have additional questions.
How do I choose the best size?
Consider what space you have for the building on your site, what kind of limitations your building department or HOA may have, plus what you plan to keep inside the building. For many customers, their only regret is that they didn’t get a larger size building. Think about a room in your house or space in an existing garage. It seems much larger when there is nothing in that space. But when you start adding large items like mowers, bikes, tools, boxes, furniture, etc. the space feels much smaller. Remember too that you’ll want to be able to easily move things in and out of your building without other items blocking the way.
Is there a difference in the products sold at Tuff Shed Factory-Direct Retail locations vs. the ones at The Home Depot?
Yes. Our different building models and series feature different specifications, sizes, available upgrades, and warranties. Our Good-Better-Best assortment of sheds and garages is available only at Tuff Shed factory-direct retail locations with the Garden Series®, Premier Series®, and Premier PRO Series(TM). All Tuff Shed buildings are designed for quality, including warranty coverage, and come with installation included in the price.
Do you sell kits?
Our building prices include professional installation by Authorized Tuff Shed installers. Our pre-fabricated building components require some specific skills, training, and tools to assemble, and are not designed to be installed by the average homeowner. Additionally, there is no warranty on workmanship or materials on buildings installed by anyone other than Authorized Tuff Shed Installers.
Prices – What’s Included?
What do base prices include?
Base prices on this website include the basic building, including installation. There is NO additional assembly cost on installed models. All construction costs are included in the base price, except for concrete slabs or footings, any required permits, any required engineering fees, and work done outside the normal installation process such as hauling away an existing structure or debris, site leveling, etc. For delivery addresses located in High Wind Zones or other jurisdictions with known special building requirements, mandated items will be added to your order, thus increasing the building price. The specifications of the base building may vary according to the building code requirements of the jurisdiction where the job site is located. Required variations from our base building plans may increase building price. Building accessories may be added to most models, but at an additional cost to the customer. Prices are subject to change at any time without notice. Please refer to Tuff Shed® building configurator at www.tuffshed.com and enter delivery zip code to see available products and current prices.
Is there a charge for delivery?
The standard delivery fee of $99 on sheds and $375 on garages will be added to orders at the time of the transaction. Fees for delivery by crane begin at $1,000.
Do I have to pay extra for installation?
No. Professional installation by an Authorized Tuff Shed install crew is included in the price.
Are there any additional costs?
We try to identify all of the costs upfront and our online configurator does a good job of identifying the line item costs of the base building, any required and customer-selected upgrades, delivery fees as well as permit and engineering fees. Sometimes, however, there can be some additional costs that have to be added to the project based on the local building requirements or the condition of the installation site. Common additional costs can include fees for site leveling more than 4″, for generator rental when the job site has no electricity available, for inaccessible installation sites that require carrying of materials long distances, and for installations that don’t have at least 18″ clearance around the structure. We ask the customer to inform us of any of these circumstances at the point of purchase. Fees relating to engineered drawings, permits, and delivery also may apply. Any such additional costs are clearly detailed for customers by their Tuff Shed sales consultant upon final review of an order.
Do you offer discounts to various groups like veterans or teachers?
We do not offer a specific discount to Vets or any other group. However, Tuff Shed proudly supports The Home Depot Foundation which focuses to improve the homes and lives of U.S. Veterans, trained skilled tradespeople, and support communities impacted by natural disasters.
Available Options and Upgrades
What types of upgrades and accessories are available?
There are numerous upgrades available for each Garden Series, Premier Series, and Premier Pro Series building model. For more information, download our upgrades catalog, visit our online building configurator or consult your local Tuff Shed sales and design consultant. Download catalog here
Can I buy a separate handle and/or hinges?
We are very proud of the patented hardware that is included on the one-of-a-kind Tuff Shed door. We will sell replacement hinges and handles to an existing customer, but these items are not otherwise for sale on an ala carte basis.
Financing and Rent-to-Own Options
What are my financing options?
Tuff Shed has some great third-party monthly payment options. RTO National offers installment loans up to $20,000 with approved credit and a No-Credit-Check Rent-to-Own option on select shed models and sizes. Special Offers
Is there a credit check?
The installment loan program through RTO requires a credit check. The Rent-to-Own program has no credit check.
What are the monthly payments?
Several factors affect a customer’s monthly payments on a financed building, including the financed amount, the A.P.R. that the customer qualifies for, and the term (length) of the loan.
What buildings are available?
All Tuff Shed factory-direct retail buildings are eligible for the installment loan program through RTO National. Not all sizes and styles of buildings are available through the RTO’s Rent-to-Own program.
Getting a building quote
How can I get a building quote?
The easiest way is to use our online building configurator on this website. You’ll be able to select from different models, and sizes and see prices and other details based on your installation zip code. You can also work directly with one of our sales and design consultants for personal guidance through the design and quoting process.
How long is a quote good for?
Prices quoted are valid through the expiration date of the promotion, but in no case shall be valid longer than seven days. Once an order has been placed, pricing is guaranteed for up to 6 months. If the installation is not completed within 6 months for any reason, Tuff Shed has the right to modify the order pricing. You will be notified regarding any price adjustment prior to installation or incurring any additional charges.
Is Concrete Needed?
Will I need to pour concrete for my building?
No, in most cases. While garages do require a concrete slab, our shed floor joist systems have more than adequate strength and moisture-resistant qualities to provide a sturdy foundation on most ground surfaces. There are some exceptions, including when local building departments require concrete, or when the shed is to be located in an area that is below the grade of the rest of your yard. Concrete is also highly recommended for two-story buildings and when the customer’s intended use for the building requires a concrete floor due to the weight or type of materials to be stored inside. In these cases, a concrete pad may be ordered from a professional contractor. Call 1-800-BUY-TUFF (1-800-289-8833) to discuss site specifications with one of our expert sales consultants.
If I do want or need concrete, how will this affect my building?
We need to know in advance if you plan to have concrete poured. Any required plans and permits MUST be obtained before that concrete is poured. Additionally, you will need to share the precise measurements of the concrete with Tuff Shed prior to the installation. See more detail in the “Pre-Installation” section of this page, or consult a Tuff Shed sales representative for more information.
Will I need anchors?
Does this need anchors/can it be anchored?
This largely depends on local building rules. Check with your local municipality if it requires a shed to be anchored to the ground. If so, anchors can be added to your Tuff Shed building order for a small fee.
What size should the slab be?
This can be a tricky question. If the shed is going to be installed with no joists or wood floor decking, then the concrete needs to be the exact size of the building, since the siding will overhang the concrete by 1.5″. For instance, on a 10’x12′ building, the concrete pad would need to measure exactly 10’x12′. If floor joists are being used, these joists are set on top of the concrete slab, so the slab can be larger than the building dimension. In either case, the customer should measure the concrete pad, and send those measurements to Tuff Shed prior to building installation. See Concrete Measurement Form.
Will I need a permit?
Do I need a permit?
This varies by building type, size, and the municipality where the installation site is located. Permits can range from simple and inexpensive to complex and expensive. The customer is responsible for paying for any required permits. Garages and larger buildings almost always require a building permit. Smaller storage sheds and sheds installed on rural building sites are less likely to require permits, but permit regulations vary according to location, and the customer should consult with the local governing body in the area where the building is to be constructed. Consult a Tuff Shed representative to determine if your project will require a permit.
Will my project be affected by my HOA rules?
There may be covenants or HOA rules in your neighborhood or regarding acceptable building size, style, height, location, etc. The customer should consult with their HOA or other neighborhood association to understand rules that may affect what types of structures are allowed.
How does Tuff Shed build?
Do you build on-site?
More like assembled on site. The building components for a job (walls, doors, rafters) are fabricated at the factory, then kitted together. An Authorized Installer crew will then pick up the kitted building, transport it to the customer site and complete the final assembly there. In some cases (for Miami, FL customers or when a building was previously used as a display), a fully assembled building is transported to the site and offloaded from a tilt-bed trailer or a crane.
Is the building delivered whole?
In some circumstances, Tuff Shed buildings can be delivered fully assembled. When a customer purchases a display building, the display will be picked up from the store and delivered to the customer site already assembled and in “as is” condition. Additionally, in some Florida markets like Miami Dade and Broward Counties, buildings are manufactured and built at the Tuff Shed factory and then the brand new building is delivered to the customer site either on a flatbed tilt trailer or via crane. In cases requiring a crane delivery, an extra fee is charged.
Do you remove old buildings?
We call this rip and haul. Our Authorized Installers don’t generally perform this service, but some of our locations can provide this service. Contact your local Tuff Shed factory-direct store to inquire.
What is the lead time?
Many factors can affect lead time, including the time of year, the type of building, any custom upgrades, the local permitting process, required engineered drawings, and the distance from the Tuff Shed factory. We know that customers are excited to get our buildings installed, and we’ll work hard to get our buildings fabricated, delivered, and installed correctly and in a timely manner. Extreme circumstances, such as the Covid-19 pandemic or natural disasters can increase lead times. Consult your local Tuff Shed store for lead times on your potential project.
Building Specs
What kind of roof will I get on my building?
Our proven construction materials and methods are the same ones used in most homes. The rafters are precut 2x4s positioned over the wall studs and joined at the center with 2″x4″ steel truss plates on both sides. This assures maximum load capacity and weight distribution. Garden Series buildings include 7/16 OSB roof decking, while Premier and Premier PRO Series buildings get upgraded 7/16 LP ProStruct Roof Decking with SilverTech Radiant Barrier technology. All three Series of Tuff Shed factory-direct buildings include roofing underlayment as a moisture barrier and a baked enamel formed steel drip edge around the perimeter of the roof decking to protect the edge of the decking from weather and to support the shingle’s edges from breakage. Garden and Premier Series include 25-Year GAF Royal Sovereign 3-tab shingles. Premier PRO Series buildings get upgraded GAF Timberline HDZ Dimensional Shingles with a Manufacturer’s Limited Lifetime Warranty. GAF Roof Warranty Information
Which wall is the width and which is the length?
The width is usually the first number shown. A 10’x12′ building, for example, is 10′ wide by 12′ in length. The width side is always the endwall, which features the point where the roof sections come together at the peak.
What type of siding do you use?
Tuff Shed uses LP® SmartSide® siding and trim as standard on our buildings. For Tuff Shed Premier Series® and Premier PRO Series(TM) buildings, we upgrade the siding to LP® SmartSide Siding with SilverTech® Radiant Barrier Technology. LP® Prorated 50-Year Limited Warranty
How tall are the different models?
Overall building heights vary by model, the width of the building, and if the customer has selected any upgrades that impact height, such as roof pitch upgrade and wall height adder. You can find standard overall heights for common widths in the specifications/sizes and prices section for each model.
How much weight can a loft hold?
A loft with 24″ On Center Joists can hold 30 lbs per square foot of typical storage. Consult your Tuff Shed rep at the design phase to increase a loft’s weight capacity for other specific use.
How much weight can the floor joists hold?
Our shed floors, with 24″ OC joists and single layer tongue and groove floor decking, are designed to support 75 pounds per square foot when the joists are placed directly onto concrete or some other firm, uniform surface; and 50 lbs psf when the joists are placed on concrete leveling blocks. Weight capacity can be increased by adding more floor joists.
What is the spacing of the wall framing?
Standard wall framing is 16″ On Center on all products except the Keystone Series® and Garden Series® buildings, which have 24″ on center wall framing.
What type of framing do you use?
Our standard wall framing and rafters are typically 2×4 dimensional lumber. The species can vary depending on the region. On larger buildings and those with an overhead loft, larger dimensional lumber (i.e. 2×6, 2×8, 2×12, etc.) can be substituted as needed. Customers can also elect to upgrade their wall framing from 2×4 to 2×6 to accommodate the insulation that they plan to add after the building installation.
What’s the spacing of the floor joists and roof trusses
Standard spacing on floor joists and trusses is 24″ on center. When required, the weight load of the roof and/or floor can be increased with additional trusses and joists.
What are the interior dimensions?
Interior dimensions (measured from the inside edge of wall framing of one wall to the inside edge of wall framing on the opposite wall) are roughly 7 inches smaller than the shed size when using a standard 2×4 wall framing. A 10’x12′ shed, for instance, has a floor area that measures approximately 9’5″ x 11’5″.
Pre-Installation
Learn about customer responsibilities, scheduling, permits, engineering, inspections and changing an order.
Types of building purchases
New buildings vs. display buildings
There are two main types of Tuff Shed® building purchases. Most purchases are new buildings, with components fabricated at our factories, then transported to the customer’s site where the building is assembled and installed. A small percentage of purchases are buildings that have been used as displays. In these cases, the fully assembled building is picked up, then transported to the customer’s site where it is delivered into place via tilt-bed trailer.
The planning process
Review your building order
This tells us how to fabricate your building, where to place items, and what colors to use for shingles and paint (if you’ve selected this upgrade).
If you purchased a display building
Display buildings are sold in “as is” condition, and can include wear and tear that ranges from minor blemishes to more significant issues such as damaged trim, missing shingles, or bent or dented floor joists. Display purchases are discounted to reflect their condition. We recommend inspecting the building first-hand to determine for yourself if the display’s condition is acceptable.
Vents
We strongly recommend adding vents to your building. Along with paint and roofing, there may be no other feature that can help your building perform better.
Insulation
If you are planning to insulate or finish the inside of your building, we need to know so that we can design the building to perform as an insulated structure.
Building permit(s)/HOA requirements
Customers need to confirm with their HOA and/or municipality for an appropriate building permits and setbacks requirements. Contact us immediately if you need help.
The Permit Process
Permit Checklist
Tuff Shed has created a permit checklist. Your local factory rep will fill this form out and mark any documents that will be required for your building.
Installation surface
What is the correct base for the building to be installed on?
The two different types of Tuff Shed floor joists are designed to be able to be placed directly on dirt, gravel, grass, concrete or other firm, dry and level surfaces. We always recommend that customers check with their municipality to see if there are any different local requirements for the building foundation.
If I do want or need concrete, how will this affect my building?
We need to know in advance if you plan to have concrete poured. Any required permits MUST be obtained before that concrete is poured. Additionally, you will need to share the precise measurements of the concrete with Tuff Shed prior to the installation. When building on a concrete pad, it’s important that this pad is square and level. See additional concrete pad measurement guidelines below.
How do I measure a concrete pad to ensure that it is square?
- Measure the length of the pad on each edge, down the middle and several spots in between
- Measure the width of the pad on each edge, down the middle and several spots in between
- Diagonally from corner to corner
How do I check a concrete pad to ensure it is level?
Use an accurate leveling device (i.e. carpenter’s level 40″ or longer) and take readings on the pad all along the perimeter.
What is a concrete curb?
In relation to a concrete pad, a “curb” is a raised concrete area generally around the perimeter of the pad where the bottom plate of the building wall sits upon and is anchored. Some garage customers prefer this option. Consult concrete contractor to determine if this is a good option for you.
What other considerations are created by having a concrete slab with a curb?
Overhead and entry door locations need to be clearly defined in advance of the having the concrete poured. It is vital that the concrete plans match those of the Tuff Shed building plans so the concrete contractor can make curb openings in the locations corresponding with doors. Concrete with curb
Leveling the building
Is your site level?
How to determine if your site is level
To accomplish this, you will need wood stakes and a string bubble level and long piece of nylon string, or a carpenter’s level and a long, straight 2×4. The string or 2×4 must be longer than the distance from the high point corner to the other three corners. Determine where the building will be placed, then drive a stake into each of the four corners and determine which of the corners appear to be the highest and the lowest points. At the high point stake place the string or 2×4 (short-edge down) on the ground and fasten it (i.e. Tie or clamp) to the high point stake. Then position the opposite end of the string or 2×4 at the low point stake. Using the string or 2×4 and the level, raise or lower the string or 2×4 at the low point stake until the level bubble floats exactly centered between the two vertical lines in the center glass vile. Now measure the distance from the ground to the bottom edge of the string or 2×4. This is the distance this first dimension is out of level. Repeat this process for the other two corners, measuring again from the high point corner, writing down your measurements. Now you can determine the distance your build site is out of level and select a method to level the site Tuff Shed®.
Figure 2. Examples of sheds using leveling tools
How do we level?
It’s important that buildings are constructed on a level site. Providing a clean and level site is the customer’s responsibility. However, for a reasonable fee, Tuff Shed® can help create a level building foundation by adding concrete blocks and wood shims beneath the structure. Tuff Shed® does NOT dig into the ground to level a building. If a small amount of leveling is necessary (up to 4”), it will be provided by Tuff Shed® at no charge.
Blocking up or “shimming” a building is not always the best solution from an appearance standpoint. Please consider the appearance and your long term satisfaction in the building when making the leveling decision. Buildings used as displays will be leveled by placing concrete blocks and wooden shims under the perimeter floor joists only. Display buildings may also include wood skids under the floor joists, which will not be removed or leveled upon delivery.



What’s the cost of leveling?
If more substantial leveling is required, the customer must choose between paying Tuff Shed® an additional fee for leveling using the concrete block and wood shim method or having the ground leveled by someone other than Tuff Shed®.
Installation day preparation
Prepare the job site
Clean the site of all debris (i.e. old tree stumps, trash, dog waste, etc) and a pathway to and from where the delivery vehicle parks.
Review access to delivery area
For new buildings, installers will need to carry building components in large sections to the assembly/installation site. If the fence gate has a top “bar”, please measure the height and width of the gate opening and provide us with this info prior to installation.
Identify and mark underground utilities
When choosing the location of the building, the customer must take into account any underground utilities that may be impacted by the delivery or installation of the building. It is the customer’s responsibility to have marked all underground utilities that will affect the delivery/installation site. Remember that these buildings and delivery trucks are heavy and that if your building was purchased with earth anchors, these anchors will be driven into the ground at a typical depth range of up to three feet deep. Many municipalities will help you locate underground electrical, natural gas, fiber optic, cable tv, and sewer. They generally will not be able to help you mark the location of sprinkler heads, underground irrigation, or septic tanks/drain fields.
For display building purchases
The building will be delivered into place via a heavy-duty truck and long, tilt-bed trailer. The truck and trailer must have a clear 12’ wide, relatively straight path from a paved road, as trailers are unable to make tight turns, similar to a boat trailer or camper. It is vitally important that there are no obstacles that cannot be navigated around, such as fences, trees, branches, playsets, or underground septic systems.
Don’t over-irrigate prior to delivery
This is especially true if your building is a display building, as our delivery vehicles are heavy, and can leave tire tracks when driving across grass or other vegetation.
Scheduling
If we haven’t scheduled already, give us a call to schedule the installation date and time range.
Pre-fabrication
For new building purchases, we will begin pre-fabricating your building several days in advance of the installation. For many installs, we begin pre-fabrication 5 business days before installation. Our outbound locations may begin manufacturing 10-12 business days before installation. At this time, we will begin placing the rough openings for items like doors, windows, and vents.
Restocking/rescheduling fee
If changes or cancellation occurs within the pre-fabrication period, a restocking/rescheduling or cancellation fee may apply. At this point, building materials have already been ordered, inventoried, and have potentially been pre-fabricated, specific to your design.
Installation day
Installers
Our installers will arrive on the site, unload materials and components, and begin to assemble your building. If you purchased a display building, our delivery driver will arrive on the site, review your desired building location, and the access route for his truck and trailer.
Age requirement
Please have someone over the age of 18 at home
Out of level sites
An out-of-level site will force our installers to stop work and collect an additional leveling fee prior to resuming.
Power sources
Our installers will need a power source so they can plug in the compressors that power their tools.
Inspect
Inspect the building before the installers leave for the day.
Weather
It may surprise you – but like most home builders, the weather seldom interferes with installation. Rain, snow, and sleet will most likely not prevent installation and will not damage the structure during installation. Ask for details.
Inspections
Inspections Checklist
Tuff Shed has created an inspections checklist. Your local factory rep will fill this form out and mark any inspections that will be required for your building.
Roof truss types
Roof trusses will vary by roof type
The type of roof truss that comes standard with your building will vary by the roof type, pitch (steepness) and building width. This is especially important on buildings starting at 12’ wide as these trusses include a bottom chord or collar tie (see diagrams below) that can impact the amount of usable space overhead. See truss examples here and contact the Tuff Shed® factory with questions.
How we paint
First coat of paint
Before being transported to the building site, the first coat of paint is applied at our factories by roller to exterior siding and trim surfaces.
Second coat of paint
The second coat of paint is applied during the on-site installation. A seasonal second coat paint discount is available in select winter markets during cold/wet months. If this discount has been applied to your order, then the installers will not apply the second coat of paint to your building during installation regardless of the weather at the time of installation.
Seasonal second coat paint discount
Customers who have received our seasonal second coat paint discount will be provided with siding and trim paint, a roller, and two small brushes. These customers should apply the second coat of paint to their building on a dry day when the temperature is higher than 35 degrees.
Display buildings
Display buildings received the first and second coats of paint prior to being put into service as a display. No additional painting will be included in the purchase.
Paint and Steel Access Doors
Whether they are standard (i.e. on a garage, PRO Studio or Pro Weekender) or added as an upgrade, Tuff Shed does not paint 3’x6’8″ steel access doors. These include manufacturer’s paint coating, and Tuff Shed only paints the door jamb of these items when the customer selects the paint option. Just as with other exterior surfaces, the customer should repaint 3’x6’8″ steel access doors every five years with high-quality exterior paint.
Appearance of materials
Displays
Display buildings are sold in “as is” condition, which can vary, ranging from minor blemishes like faded paint to more significant issues such as damaged trim, missing shingles, and dented or bent floor joists.
Roofing nails
It’s not a mistake that nails are poking through the roof on the inside of your building. This is necessary due to building codes requiring shingle nails to “pierce the roof decking material” and does not affect the performance of the roof.
Galvanized steel floor joists
Most of our sheds include 16-gauge, hot-dipped galvanized steel floor joists, which are designed to be placed directly on any firm, level surface. White “chalking” on the steel – this appearance is normal and does not affect the performance of the steel or the 40-year industry-rating on the material.
Exposed steel
These joists are designed to withstand the elements and are exposed after installation. Some customers prefer to cover the steel with “skirting” made from the siding. While we can add skirting, we don’t recommend it, since wood siding material contacting the ground can wick up moisture into the building.
Small rectangular holes in the steel
During production, small vent holes are punched into the steel. These holes allow for airflow beneath the building. Snap-in screen vents are available as an inexpensive upgrade.
Lumber
We use dimensional lumber for wall and roof framing that has been dried, then stored in a controlled environment (our factories) prior to installation. It is unlikely that this wood will have a uniform appearance, and may have blemishes or “waning and knots”. This is normal and will not affect the structural integrity of the building.
Weathertight or airtight
We strive to make the building weathertight. But they are not airtight. Air and mice can infiltrate your building as they can your home.
Post-Installation
Request a warranty repair, purchase keys, maintenance tips, moving or leveling a shed.
Proper care and maintenance
Keep your building on the level
When normal ground settling occurs, it can affect your tuff shed building, making it difficult to open, close or latch the door. This is not a warranty issue, but in most cases, the building can be easily re-leveled by the customer or for a reasonable fee by Tuff Shed®.
Protect your floor
Do not add rubber mats or vinyl flooring inside as they can create a serious moisture and rot issue. Do not block floor track vent holes.
Redirect water
Water is the enemy of most structures. Take care to redirect water from your building whenever possible. Rainwater runoff from other structures and misdirected irrigation systems can damage your Tuff Shed® building and is not covered by warranty.
Re-paint regularly
Painting is one of the easiest ways to protect the exterior wood surfaces of a Tuff Shed® building. Your building’s warranty coverage requires that the building be re-painted every five years. We recommend using high-quality materials like glidden paints.
Do I need to repaint the shed?
Yes. Repainting the building every five years is important for your building’s longevity and required to maintain the warranty.
What paint should be used for exterior touchups?
Use a quality, exterior paint, such as Glidden Professional.
Leveling
The blocks and shims used are ugly, how do I cover them?
When a building has been leveled with concrete blocks, the floor joists don’t sit flush with the ground. Customers can backfill the ground at the base of the shed using a material such as crushed gravel. We recommend not covering the vent holes, however, since these allow for airflow under the building.
The ground has settled under my building. Can you relevel it?
We can relevel for a fee. Please contact our local factory for a quote on pricing and lead time.
Moving a Shed
Can my Tuff Shed storage building be moved?
It’s possible, depending on the size of the building. Tuff Shed, however, does not offer a shed moving service.
Who should I contact to move my shed?
There are shed moving services available in most markets and can be found by doing an online search.
Animal control
How do I cover the vent holes for insects?
Floor track vents are an inexpensive and easy to install option, and can be purchased from Tuff Shed.
How do I keep animals from getting under my shed after levelling on blocks?
When a building has been leveled with concrete blocks, the floor joists don’t sit flush with the ground. Customers can backfill the ground at the base of the shed using a material such as crushed gravel. We recommend not covering the vent holes however, since these allow for airflow under the building.
Purchasing Aftermarket Items
Can I order new keys?
Yes. Use the contact form found on this page to make your request. We’ll need to verify your customer record and address.
Can I order ramps or other accessories?
Some upgrades can be ordered after the building has been installed. Contact your local factory or fill out the contact form on this page to inquire about specific upgrades.
I want to repaint my shed, can I order the paint from Tuff Shed?
In most cases, we can tell you the brand and color of the paint that was applied to your shed. Our factory inventories aren’t really set up to sell paint ala carte, so the customer is better off sourcing paint at a retailer that has a paint department, such as The Home Depot.
Building Appearance
There are nails poking through the inside of my roof
This is intentional, as it is required by building code. The shingle nails must penetrate the roof decking material.
The 2x4s inside my building have knots and blemishes
This is normal and will not affect the structural integrity of the building. We used dimensional lumber for wall and roof framing that has been dried, then stored in a controlled environment (our factories) prior to installation. It is unlikely that this wood will have a uniform appearance, and may have blemishes like waning and knots.
I can see the steel foundation of the shed
This is normal. Most of our sheds include hot-dipped galvanized steel floor joists, which are designed to be placed directly on any firm, level surface.
My shed’s steel foundation is punched with rectangular holes
This is by design. During production, small vent holes are punched into the steel, allowing for airflow beneath the building. Snap-in screen vents are available for an inexpensive upgrade.
There is white chalking on the steel foundation on my shed
This appearance is normal and does not affect the performance of the steel or the 40-year industry rating on the material.
What if I want to hide my shed’s foundation
Some customers prefer to cover our steel or wood joists with “skirting” made from siding. We don’t recommend this practice, since wood siding material contact the ground can wick up moisture into the building.
Paint
I purchased the paint upgrade, but my shed only received a single coat of paint
A Seasonal Second Coat Paint Discount is available in winter markets during cold/wet months. If this discount has been applied to your order, then the installers will not apply a second coat of paint to your building. Check your order to see if your order included this discount and contact your local Tuff Shed factory with questions.
What is the Seasonal Second Coat Paint Discount?
This is a discount for customers who have received our Seasonal Second Coat Paint Discount will be provided with siding and trim paint, a roller, and two small brushes. These customers should apply the second coat of paint to their building on a dry day when the temperature is higher than 35 degrees.
I didn’t receive the Seasonal Second Coat Paint Discount, but my shed still only got one coat of paint
Keyless Door Handle Programming
Warranty Repairs
What should I do if I have a warranty request?
Contact your local factory by calling 800-289-8833 or submit the form found on this page.
If my shingles blow off the roof, is this covered by warranty?
That depends. In the event of a natural disaster such as a tornado, hurricane, hail, etc., shingles that blow off the building would be covered by the customer’s homeowner’s insurance and are not covered by the Tuff Shed warranty. If the shingles blow off a Tuff Shed building under normal conditions and use, then the workmanship clause in our warranty would cover the reinstallation of those shingles.
What if I have an issue with the door handle not working properly?
It is possible that over time the door handle might need to be adjusted, this is covered under the warranty.
My handle is broken and needs to be replaced
Even though our door handles are extremely heavy-duty, we sometimes hear from customers who have a broken handle. If the handle is damaged due to normal wear and tear, then replacement would be covered by the Tuff Shed warranty. If the handle is damaged due to theft, misuse, or abuse, then the customer can purchase a replacement handle. In cases like this, we will want to verify the customer account and address.
Issue with door sagging or not closing properly
When the door sags it is typically due to the settling of the ground underneath the shed. Sinking/settling is not covered by our warranty. You can contact the local factory for a quote on re-leveling. If the door is not closing properly due to a problem with the hardware, then this issue would typically be covered by warranty.
Issues with door hardware fasteners
If a fastener malfunction on door hardware like handles and hinges, this is covered under warranty.
My door hinges are bent
Our hinges are designed to hold up to 500 pounds each. Bent hinges are covered by the Tuff Shed warranty if the damage is due to normal wear and tear. Damage that is caused by misuse or a natural disaster such as a tornado, hurricane, hail, etc., would be covered by the customer’s homeowner’s insurance and are not covered by the Tuff Shed warranty.
Finishing the inside of a Tuff Shed building
How do you insulate a building?
There are different approaches to insulating a building, and these can vary by climate. Consult a local insulation contractor for ideas. The common first step is to add a vapor barrier between the siding and the insulation. Tuff Shed customers should select house wrap at the time of purchase if they plan to add insulation to their building after installation.
Can I add floor covering?
Can I paint over the inside of the siding and framing? If so what paint type?
Contact Us
I have a problem with my building and need to get in touch with the local factory
Contact your local factory by calling 800-289-8833 or submit the form found on this page.
I cannot reach my local factory by phone
Please fill out and submit the contact form found on this page. This will allow us to more easily track your issue.
I’m waiting for a refund; who do I contact?
Contact your local factory by calling 800-289-8833 or submit the form found on this page.